


Four dynamite steps for lighting a fire under your improvement program
What do leaders need when they are starting out in improvement? They need some strong tips to help them understand what they are trying to achieve and some tools to get started with. I’m a big believer in giving people simple, straightforward options when it comes to lean and starting an improvement program is no different.

Lean Leadership – Using PDCA to drive improvements to the next level
It happens in every system. You find a problem, record your current state, experiment towards the target vision, come up with a fantastic solution and feel that great sense of […]

Lean Leadership – Why you must celebrate those tiny lean successes
I’ve heard it many times from really successful managers. “We’re doing improvement, we’re just not documenting it.” My eyebrows always raise a bit when I hear this particular phrase. That’s […]

Clear that Desk! – Tips on achieving a more minimalist, lean workspace
Earlier this year I wrote a post about managing workplace clutter and my own personal quest for a minimal ‘lean’ workspace. At the time, I wasn’t sure how easy my seriously pared down workspace was going to work out. Would I be buried under clutter a few months later, or constantly frustrated by having nowhere to put anything?

Lean is not an “off-the shelf” commodity
No one’s going to buy an improvement program just because a version of it works for someone else. Here lies the misconception. If someone has to sell you an improvement program, you’re probably not ready for it.

When starting out with Lean Key Performance Indicators (KPIs) – Less is More
In a post I wrote earlier this year, I talked about the key pitfalls of visual display boards and some tips for avoiding them. I briefly mentioned what I believe […]

Lean Leadership – The importance of having a clear target vision for your lean transformation.
One of the key pitfalls that companies fall into as they embark on a lean transformation is failing to establish a clear vision of what lean will look like when implemented in their business.

Improve your 5S culture by lowering your standards
By setting a perfect standard we can sometimes make the standard impossible to realise. It's much better to set a realistic standard that requires some improvement to achieve but doesn't necessarily ask for perfection all at once.
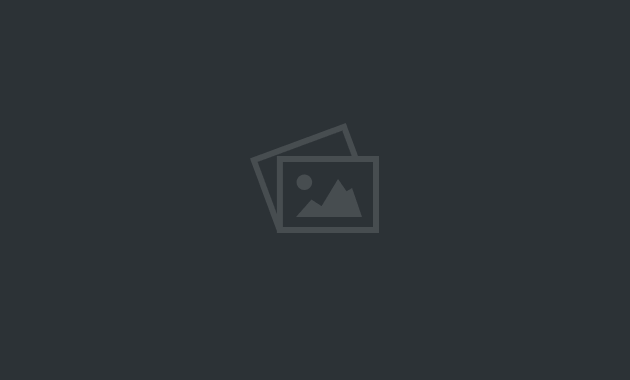
Lean Leadership – How culture grows through empowering people to change their own processes
As I watch our team members explain how they or their team personally changed their own work processes for the better, I am reminded both of how far the culture has come in nearly three years and of the truth that lean culture grows out of the empowerment and commitment of people.